A Cultura Lean, ou como também é chamada na indústria, a Lean Manufacturing (Manufatura Enxuta), foi desenvolvida originalmente pela Toyota na década de 1950, e até os anos 1980 passou por aperfeiçoamentos no seu sistema. Desde então, despertou um interesse grande de empresas dos mais diversos portes e segmentos.
O Lean trata-se de um corpo de conhecimento, cuja maior essência é a capacidade de eliminar desperdícios continuamente e resolver problemas de maneira sistemática.
A seguir, saiba mais sobre o que é Cultura Lean, seus benefícios e como aplicá-la no chão de fábrica.
Relacionado: Lean Manufacturing: Pequenas mudanças, grandes resultados
Quais são os princípios da Cultura Lean?
A Cultura Lean busca, acima de tudo, melhorar a eficiência e produtividade das empresas, eliminando desperdícios e otimizando processos. O objetivo é entregar mais valor ao cliente com o menor uso possível de recursos, seja em fábricas, escritórios ou outros ambientes de trabalho.
Para guiar essa transformação, a Cultura Lean se baseia em princípios claros que ajudam as empresas a estruturar suas operações e alcançar resultados consistentes.
Confira os principais princípios:
- Valor definido pelo cliente: identificar o que é realmente importante para o consumidor. Tudo que não agrega valor deve ser eliminado ou ajustado.
- Mapeamento do fluxo de valor: visualizar todas as etapas do processo, desde o início até a entrega final, para identificar gargalos e eliminar desperdícios.
- Fluxo contínuo: garantir que os processos funcionem sem interrupções, permitindo que as atividades sigam de maneira ágil e eficiente, sem acúmulo ou espera desnecessária.
- Produção puxada: alinhar a produção à demanda real, evitando excesso de estoques e superprodução, o que economiza recursos.
- Melhoria contínua (Kaizen): incentivar a busca constante por melhorias em processos, produtos e métodos de trabalho, promovendo inovações e resultados melhores.
- Respeito às pessoas: aumentar o engajamento de equipes, valorizando sua participação e promovendo um ambiente de trabalho colaborativo e confiável.
Como implantar a cultura Lean na indústria de alimentos e bebidas?
Introduzir essa cultura à indústria pode ser um diferencial competitivo poderoso. O segredo está em adaptar os princípios Lean ao contexto do setor, que envolve alto controle de qualidade, regulamentações rigorosas e demandas variadas do consumidor.
Para começar, é fundamental que a implantação seja planejada de forma estratégica, envolvendo todos os níveis da empresa.
Confira os passos principais para transformar sua operação com a Cultura Lean:
1. Defina o propósito e os objetivos do negócio
Antes de qualquer mudança, é essencial entender o propósito central da empresa e alinhar os objetivos estratégicos. Seja reduzir custos, aumentar a eficiência ou atender a novas demandas do mercado, esse direcionamento servirá como base para todas as ações.
“Para aplicar o Sistema Lean é preciso ter um propósito definido, rever processos, aplicando as várias ferramentas Lean, capacitar as pessoas, mudar o sistema de liderança e o modelo mental”, salienta o Conselheiro e Senior Advisor do Lean Institute Brasil (LIB), Flavio Augusto Picchi, em entrevista ao Food Connection (2017).
Primeiramente, conforme cita o especialista, é preciso ter bem definido o que é preciso melhorar para tornar a fábrica mais competitiva. O Lean precisa ser pensado como uma metodologia para apoiar objetivos de negócio.
“Algumas empresas dizem que querem aplicar o Lean porque ouviram dizer que é uma metodologia muito efetiva e, começando desta forma, já se inicia o processo de uma forma equivocada”, esclarece Picchi.
Dessa forma, antes de implementá-lo, é importante que o empresário faça perguntas como:
- A indústria não está sendo competitiva?
- Ela não está conseguindo entregar os produtos dentro dos prazos?
- É preciso reduzir custos, devido à concorrência internacional?
Respondidos esses questionamentos e identificando-se os problemas, pode-se implementar o Lean na indústria.
2. Entenda o valor do negócio para o cliente
Uma vez definido o propósito, tendo em vista que o maior objetivo da Cultura Lean é propor uma mudança de paradigma, faz-se necessário seguir para a segunda etapa que é a mudança de processos.
No chão de fábrica, para promover essa mudança é preciso entender o que é valor para o cliente. É necessário saber se o público-alvo da indústria em questão busca produtos mais flexíveis, entrega com o tempo adequado, produtos novos, de melhor qualidade, por exemplo. Para isso, é preciso analisar processos desde a manipulação da matéria-prima até o produto final.
Compreender o valor percebido pelo cliente ajuda a eliminar etapas ou processos que não agregam benefícios diretos.
Relacionado: Comunicação com o cliente na indústria alimentícia
3. Reorganize o chão de fábrica
Outro ponto que cabe destacar para que o sistema seja implantado com sucesso diz respeito à organização do chão de fábrica. A organização da produção em células acaba se tornando um importante passo, bem como uma mudança no modo de produção, priorizando-se a fabricação por demanda, de modo a não deixar os estoques parados.
Portanto, analise o fluxo de trabalho e reorganize o layout para minimizar deslocamentos desnecessários, gargalos ou tempo ocioso. A ideia é criar um ambiente onde os processos fluam de forma contínua e eficiente, maximizando a produtividade e reduzindo desperdícios.
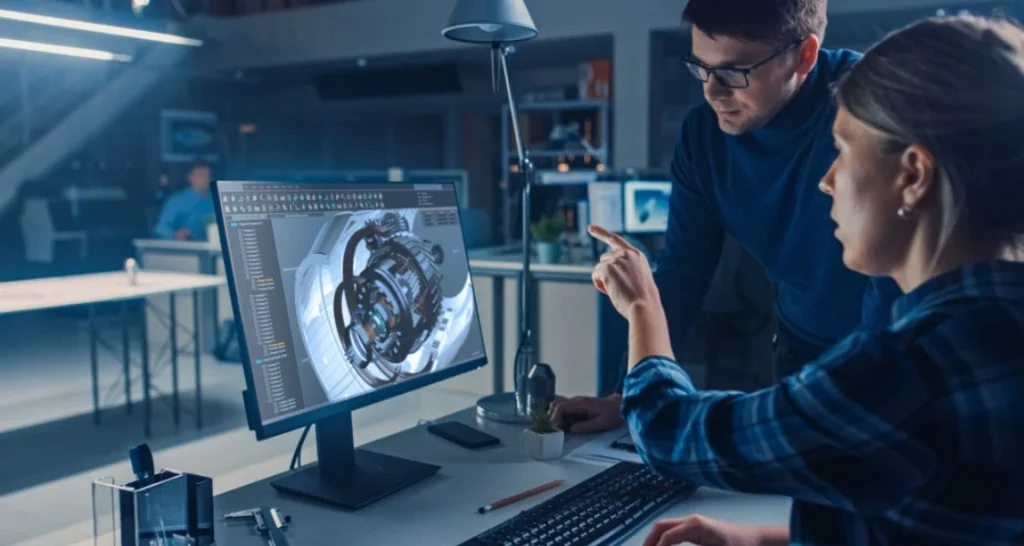
4. Capacite a equipe
Depois do foco nos processos, é preciso preparar as pessoas. “O Lean é muito forte em expor problemas, inclusive, fazendo uma gestão visual, de modo que os próprios operários possam, em conjunto com o seu Team Leader, solucionar problemas na base”, destaca Picchi.
Nenhuma transformação é possível sem o envolvimento e a capacitação dos colaboradores. Invista em treinamentos para que todos compreendam os conceitos Lean e saibam aplicá-los no dia a dia. Além disso, incentive a participação da equipe na identificação de problemas e na busca por soluções.
5. Transforme o papel da liderança
O último aspecto fundamental na implantação da Cultura Lean diz respeito a uma mudança mental. Ela propõe a quebra do modelo tradicional de modo a expor o problema para os gestores, buscando as melhores soluções para melhorar a produtividade.
Os líderes precisam atuar como facilitadores, promovendo uma cultura de melhoria contínua e engajamento. Em vez de apenas gerenciar, eles devem inspirar e dar suporte aos colaboradores para que a mentalidade Lean se torne parte do cotidiano da empresa.
Como medir a eficácia da Cultura Lean na empresa?
Medir a eficácia da Cultura Lean é essencial para garantir que os princípios de melhoria contínua e eliminação de desperdícios estejam gerando os resultados esperados. Isso envolve a aplicação de ferramentas e indicadores específicos que proporcionam uma visão clara sobre o desempenho dos processos e a geração de valor.
Algumas formas de implementar essa medição de forma estratégica envolvem:
1. Defina e monitore Indicadores de Desempenho (KPIs)
Os KPIs são fundamentais para avaliar aspectos cruciais como:
- Eficiência operacional: identificar gargalos e promova fluxos mais ágeis.
- Qualidade do produto: monitorar defeitos e retrabalhos.
- Custo de produção: avaliar economias geradas pela redução de desperdícios.
- Satisfação do cliente: verificar se as mudanças atendem às expectativas dos consumidores.
Os KPIs devem ser definidos de acordo com os objetivos estratégicos da empresa e revisados regularmente para refletir as mudanças no ambiente de negócios.
Relacionado: Como melhorar KPIs para impulsionar a eficiência das fábricas
2. Use o mapeamento de processos
O mapeamento de processos, especialmente o mapeamento de fluxo de valor, permite visualizar cada etapa do trabalho. Essa ferramenta ajuda a:
- Identificar atividades que realmente agregam valor.
- Eliminar tarefas redundantes ou que causam desperdícios.
- Tornar os processos mais transparentes para a equipe.
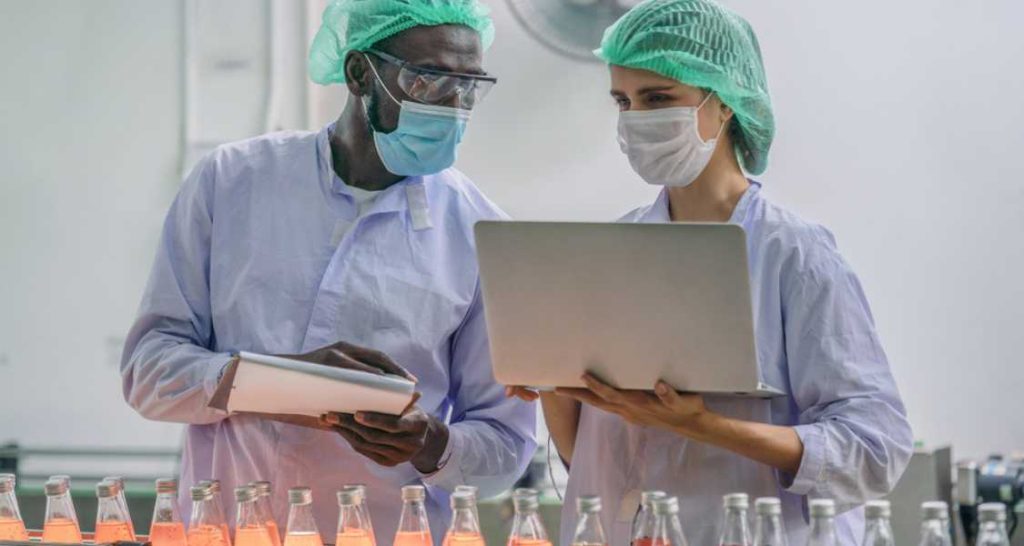
3. Implemente o 5S para melhorar o ambiente de trabalho
A metodologia 5S (Seiri, Seiton, Seiso, Seiketsu, Shitsuke) promove a organização e eficiência no local de trabalho. Ao medir sua aplicação, é possível identificar ganhos como:
- Redução do tempo gasto em tarefas rotineiras.
- Aumento na produtividade da equipe.
- Melhoria da segurança e ergonomia.
4. Fomente a melhoria contínua com Kaizen
Sessões regulares de Kaizen incentivam a equipe a identificar problemas e sugerir melhorias incrementais. Além disso, ajudam a:
- Criar uma cultura de participação ativa dos colaboradores.
- Resolver desafios operacionais de maneira ágil.
- Garantir que as mudanças implementadas sejam sustentáveis.
5. Meça a satisfação do cliente
O cliente é o principal beneficiário das práticas Lean. Utilize pesquisas, análises de feedbacks e índices como o Net Promoter Score (NPS) para entender como as melhorias impactaram a experiência do cliente, o nível de lealdade à marca após as mudanças e quais áreas ainda precisam ser aprimoradas.
6. Monitore a Eficiência dos Equipamentos (OEE)
O indicador Overall Equipment Effectiveness (OEE) mede a eficácia dos equipamentos, considerando disponibilidade, performance e qualidade.
Esses dados permitem priorizar investimentos e intervenções técnicas de maneira estratégica.
7. Apoie-se na análise de dados
Utilizar análises de dados ajuda a identificar tendências e padrões. Isso facilita a tomada de decisões baseadas em evidências e o ajuste contínuo das iniciativas Lean.
Relacionado: Como fazer a gestão e o controle de estoque de alimentos na indústria?
Benefícios da cultura Lean para indústria alimentar brasileira
O Lean traz muitos benefícios, uma vez que a metodologia muda completamente o paradigma da indústria, já que se passa a olhar com mais afinco o fluxo de valor do chão de fábrica.
Os principais são:
- Aumento de produtividade: reduz gargalos e otimiza processos, liberando colaboradores para áreas que precisam de mais atenção.
- Redução de estoques: minimiza excessos, promovendo uma gestão de processos mais enxuta e econômica dos recursos.
- Cultura organizacional: cria uma equipe mais engajada e capacitada para resolver problemas e buscar inovações.
- Redução de custos: elimina desperdícios em todas as etapas, desde a matéria-prima até a entrega do produto final.
- Melhoria na qualidade: garante processos mais eficientes, reduzindo erros e elevando o padrão dos produtos.
“O maior benefício, a meu ver, é o desenvolvimento contínuo das pessoas para que elas colaborem na melhoria dos processos”, comenta o especialista do Lean Institute Brasil.
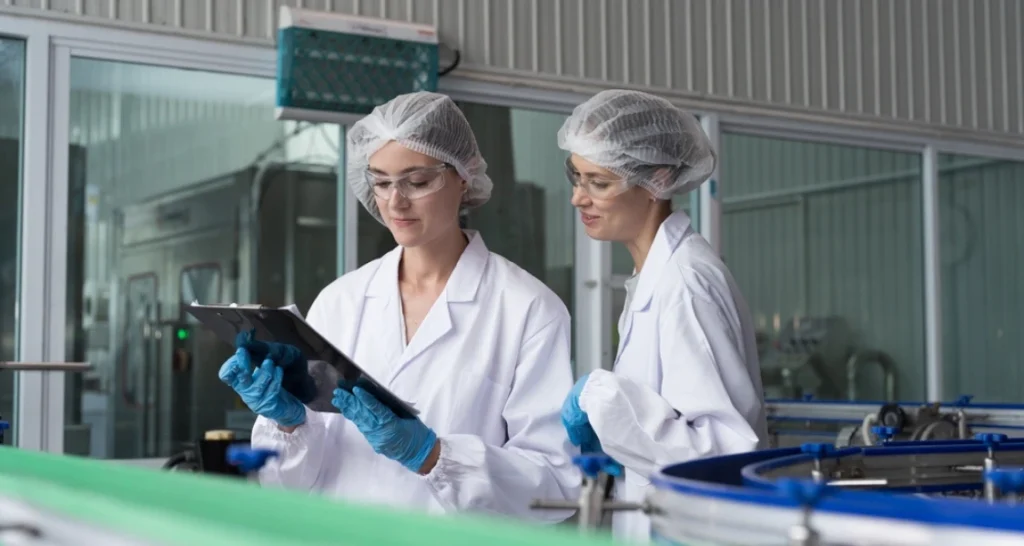
A Cultura Lean oferece uma abordagem transformadora para a indústria alimentícia, trazendo benefícios que não apenas otimizam os processos internos, mas também fortalecem a capacidade das empresas de atender às demandas do mercado com mais agilidade e eficiência.
Implementar os processos Lean é uma ação gradual que exige planejamento, engajamento e um compromisso com a melhoria contínua. Contudo, os resultados podem representar uma vantagem competitiva significativa em um mercado tão dinâmico como o brasileiro.
Comece identificando as áreas que mais precisam de ajustes e veja como essa estratégia pode levar sua empresa a novos patamares de desempenho e sucesso.